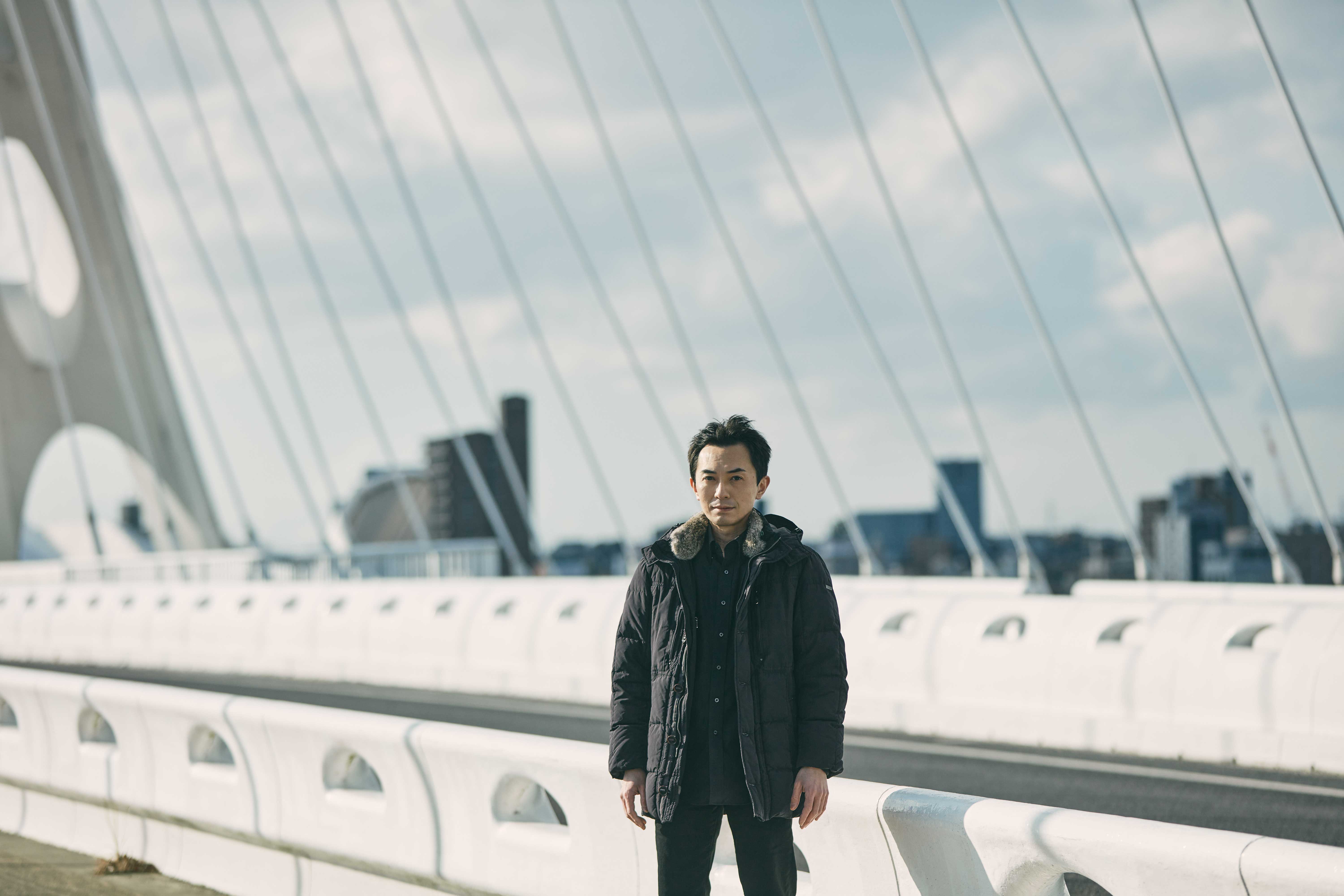
UT aim
Ken Kubota
PROFILE
Ken joined UT Aim in 2010 at the age of 30. After eight years as an operator and in inspection work for manufacturing equipment at a semiconductor company in Kasaoka City, Okayama Prefecture, he applied for the internal job change program. From 2018, he has been responsible for the sequential part process and assembly of suspension parts at a major car manufacturer in Toyota City.
I didn't last for a long time for any job in my twenties.
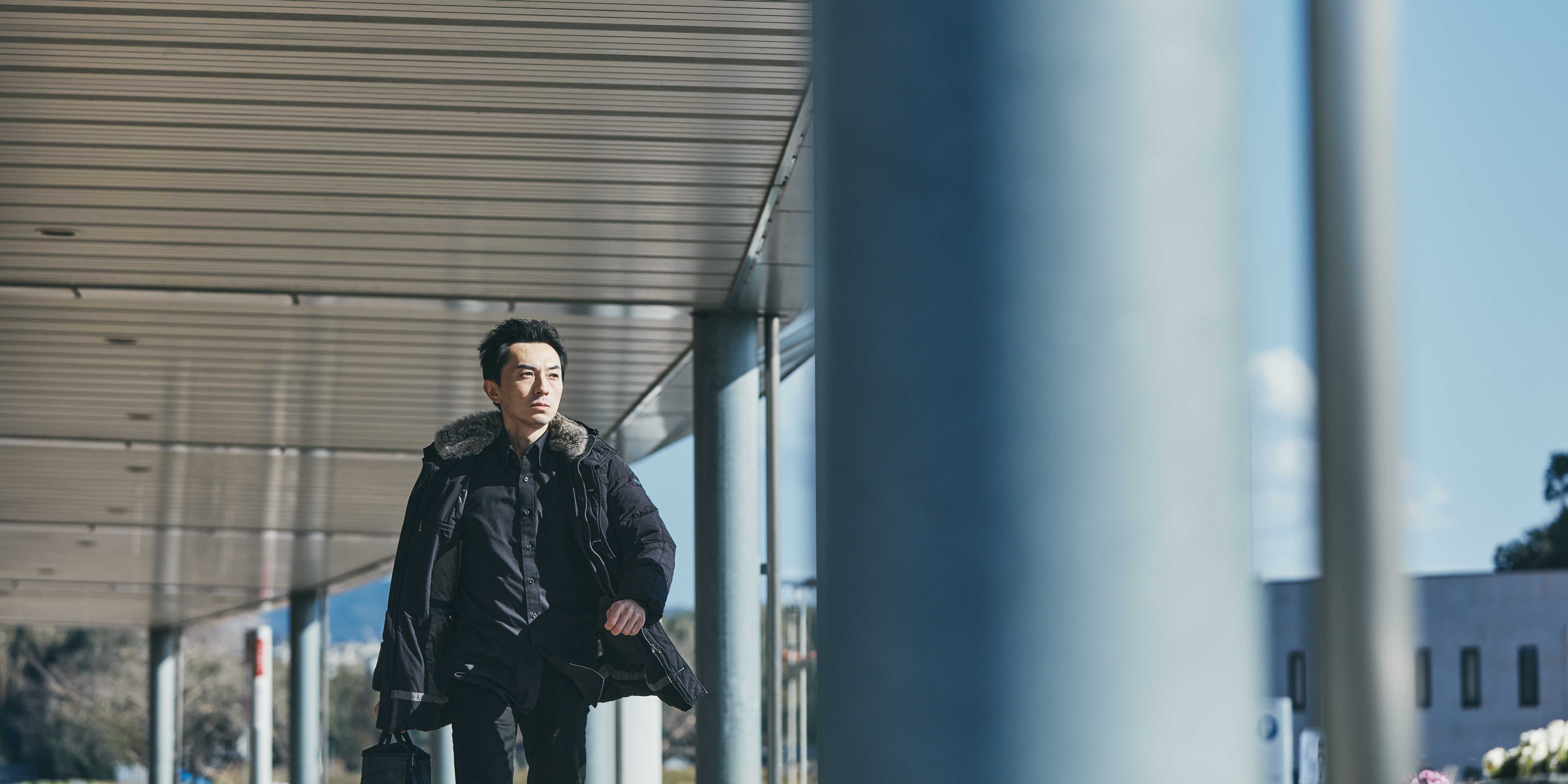
I think I always ran away. After leaving the school, I keep switching jobs, including work at restaurants and factories and as concert staff. With no particular motive, I entered UT Aim because I was fed up with my previous metal processing job and that I was attracted to the good working conditions. Although a bit embarrassing to say it, I felt I should work hard as I was becoming 30 years old, and just got married two years ago (laughs).
After joining UT, I was assigned as an operator, and given the job of inspecting semiconductor manufacturing equipment. I mechanically repeated the tasks in the defined steps every day. I simply did so without making too much efforts. However, one day in the third year, the manager told me:
“Kubota, how about becoming a subleader next month.” I had no reason to decline because I was comfortable with the workplace and my working conditions would be better. Without thinking deeply, I accepted the offer and coolly got on with the subleader job. Then in two years, I was appointed to be a leader. Around this time, I changed my attitude. “Until now, UT has given me a role and helped me increase my value. From now on, I’ll do my best to add even more of my value!”
Aiming to become a full-time employee of a world-famous automaker.
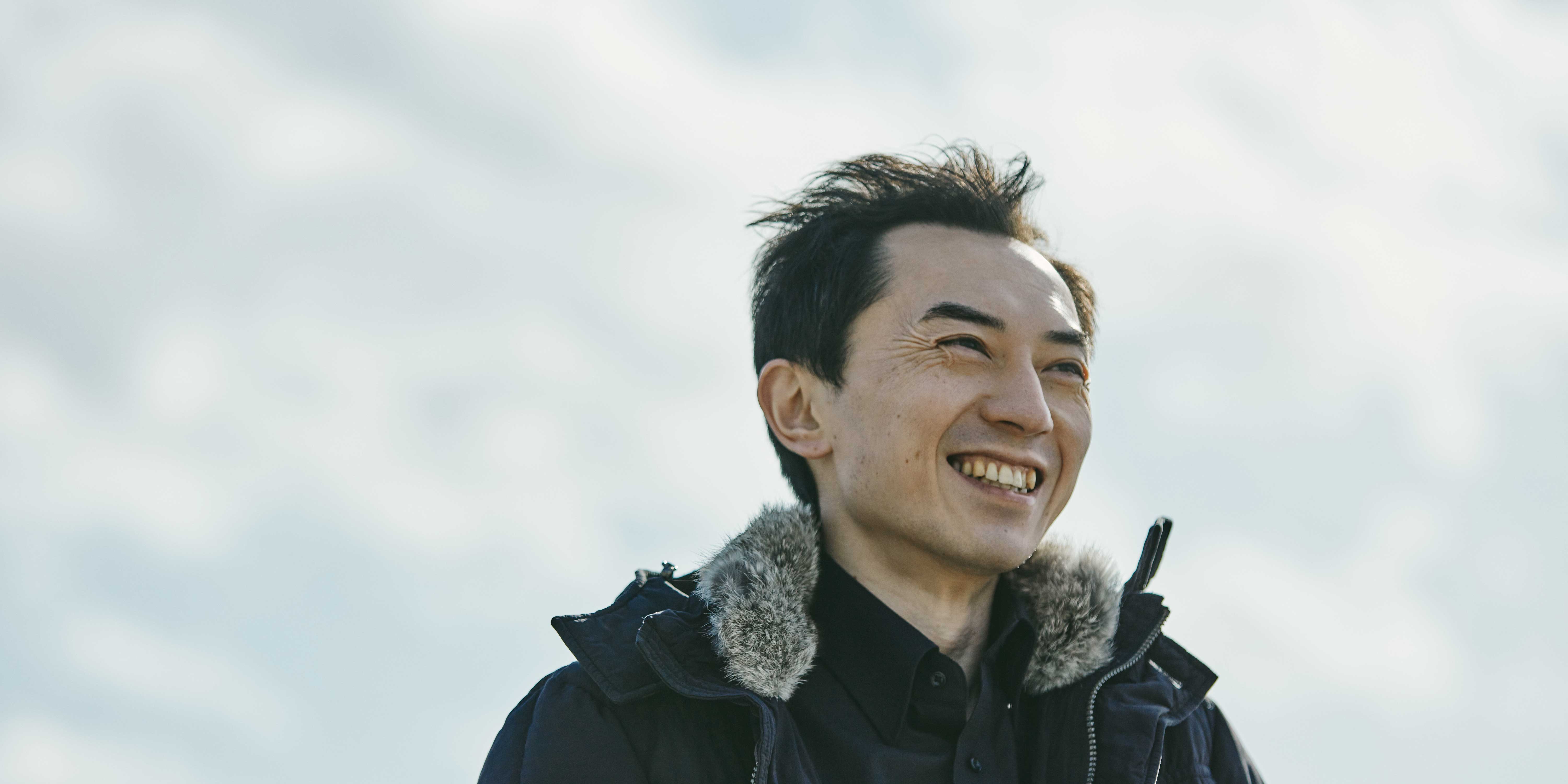
In the eighth year after I joined UT Aim, I learned about the Toyota Challenge in an internal PR document. This sounded really attractive as it would allow you get exposed to the world’s top manufacturer’s technologies and ideas, as a member of a team assembling automobiles. Moreover, this program offered the potential to become a full-time employee of that major automaker. I intuitively felt: “Now is a chance. I’ve got to take this opportunity!”
The first thing I felt at the worksite was the ease of working. The staff there seemed to have some leeway as to how to do the work and there was a positive atmosphere. Looking back, I had looked at the negative side of my boss and colleagues and made cowardly excuses in my twenties. I now know that the work cannot be done by one person. I try to look at the positive side of my peers and to frequently talk with them, in order to overcome my awareness that I am not good at making relationships with people.
My current job requires physical strength and concentration, and it’s not easy. Still, there’s an atmosphere that makes you want to try harder than you are asked to do. In fact, my proposal on a layout change (arranging components according to the order of assembly) was adopted, and the efficiency was increased by about 30 minutes per day. I want to enhance my value as a person who suits every need of the workplace and my goal is to be a full-time employee! A casual comment from the supervisor is a great encouragement for me. “Kubota, you do a great job. Thanks for your help.”